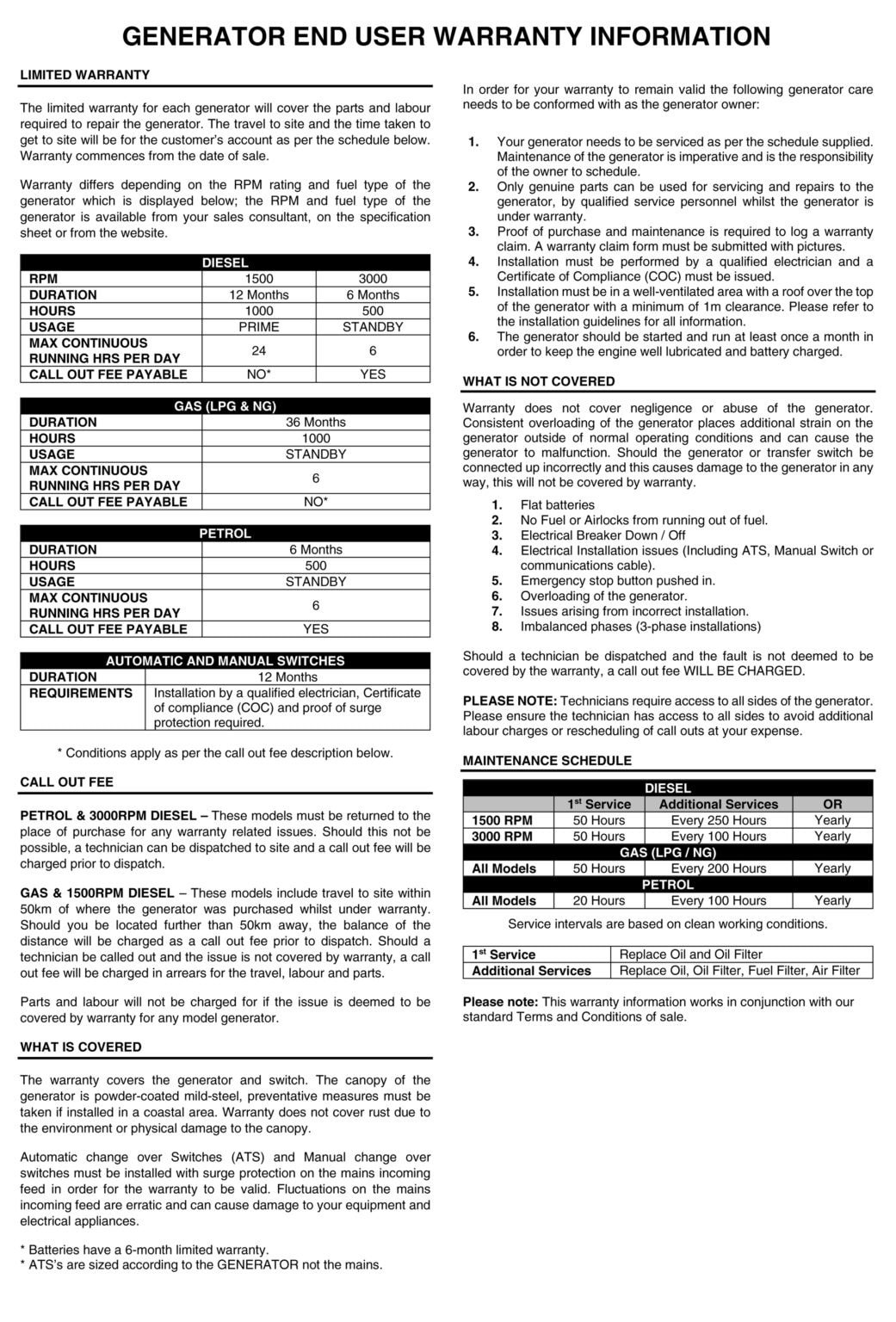
Overloading & Underloading Generators
A general overview of diesel engine design and operation
1) Preamble Since inception there has been a constant push to improve the design and operational efficiency of the diesel engine, whether mobile or stationary. This has led to more and more “stress” being applied to engines in order to extract the highest amount of power from the fuel used. Diesel engines prior to 1960 were known as 35% engines (producing only 35% of their available power) whereas modern engines are 70% to 85% engines.
2) Aspiration In the beginning all engines were naturally aspirated, I.E., no aids were fitted to increase the amount of air in the cylinders of the engine by artificial means. Such engines were, in the main, able to operate at no load to very minor loading as they were relatively low compression machines which could rely on the inherent spring loading of the piston rings to seal the compression and the ignition stroke of the engine.
Presently most diesel engines are fitted with high delivery turbochargers which are exhaust gas driven and, when the engine is operating at a minimum of 50% loading will supply sufficient air into the combustion area to ensure that all of the injected fuel is burnt. The turbocharger when operating in this manner will increase the compression inside the cylinder to the degree that the engine can no longer rely on the inherent spring capacity of the piston ring to seal the cylinder during a compression or ignition stroke. This has caused a redesign on the piston rings on a modern diesel engine to ensure that a small amount of compression air “bleeds” past the inside of the compression ring and forces it against the bore of the cylinder to seal it against the high compression experienced.
3) Low loading consequences
Considering the above it will be seen that running a modern turbocharged diesel engine at very light loading will result in the rings of the engine not sealing correctly which will allow compression air to bleed past the ring band and pressurise the sump of the engine, it will also allow any unburnt fuel to run down the bores of the engine into the sump which will dilute the lubricating oil in the machine. This along with the air pressurisation of the sump will lead to traumatic mechanical failure of the machine up to and including a broken crankshaft or a connecting rod. If the engine is fitted with an aftercooler this will only exacerbate the situation and the damage can occur in a very short time, possible as few hours run as 20 to 25 hours.
Conclusions & Warranty Implications
When taking all of the above into account it will be obvious that a stationary diesel engine must be run, at least, at 50% and preferably 65% of its rated output to avoid damaging the engine. It must be noted that all manufacturers’ warranties do not cover damage to their engines caused by low load running it is therefore in the client’s interest to ensure that their machine is correctly loaded.